. |
|
|
**** Impregnating and drying machine for ****
* Advantages of SHINETEC Horizontal Type Impregnating & Drying Machine |
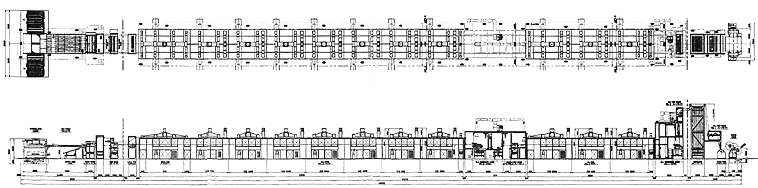
Shinetec's special nozzle have been used as horizontal type dryer's hot air nozzle to impregnating & drying machines for insulating board and decorative board in order to production, also to film coating machines etc.
Dimension of nozzle width direction in machine is wide width of over +300 - 400 mm against max. treatment material width. And due to both use the slit nozzle and round nozzle, it is very strong to support the material, and floating situation is very good even wide width of 3,000 mm. (Material is no-flapping)
As you know, quality of floating property is judged in compliance with no-tension, no-vibration at selvedge and no-meandering of material
It can be get evenness air speed against width direction.
It can be treated from thin material to heavy material due to achieve the minimal tension. Also can be corresponded at wave part of inside the dryer against fluctuate material tension.
It can be conveyed easily the heavy materials by special floating system even air speed of max. 35 m/sec. at round nozzle section.
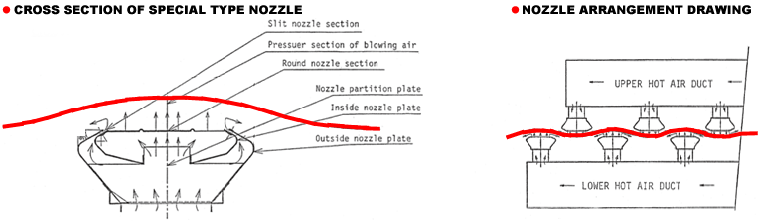
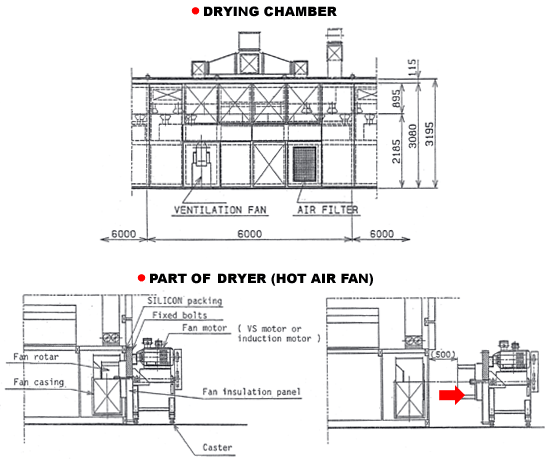
* Advantages of SHINETEC Vertical Type Impregnating & Drying Machine |
Shinetec's Vertical type dryer has both types of drying heat source with hot air system (Parallel and counter flow) which occupy 70% ~ 80% of necessary calorie for drying, and radiant system deposited ceramic of far-infrared ray radiation on the surface which impregnated resin can be easily absorbs with radiates the wavelength for effective drying and curing.
Shinetec's Vertical type dryer is possible to transport the materials from 11 g/m2 of the very thin thickness to 210 g/m2 of thick material by making good use of speed control motors and tension controlling in the drying chambers with a steady hot air amount balance.
Each devices including the dryer are arrangement and construction it to be easy maintenance in addition by past results and the experience.
After the pre-impregnating, material completely removes air from the web (Sky penetration), and knife roller make impregnating value and surface finish extremely.
It has been the recent tendency that production of thin material such as 15/25/50 g/m2 are becoming indispensable situation from the conventional thick materials. Main line of impregnating section for the conventional thick glass material has been squeeze roller system, which is mass production type with high speed comparatively. However, for this thin glass material tendency, resin impregnating section becomes the face control type by all means and the separating sharpness of the material from the roller is no good, so it is hard to improve the accuracy of impregnating face.
Shinetec's knife roller unit can solve these problems and we got the good reputation that this type is the best for impregnating the thin glass material from each user of our supplied machine. Of course, we can get similar impregnating face in the operation of the thick materials such as 100 g/m2 and 210 g/m2. Clearance of knife roller (or squeeze roller) can be control automatically for right and left individually and Degi-micro meter can be controlled with a unit of 1-micron.
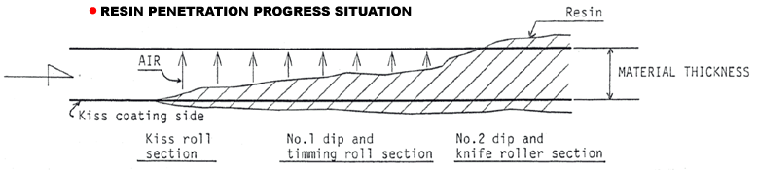
Most resins have remarkable absorption bands in the Far-infrared wave length range. Shinetec's radiation curing oven makes use of this principle. Far-infrared ray Radiation heats the resin coat layers from the inside, for effective drying and curing and at a high production rate.
The dryer that is indispensable unit to dry curing of resin is big key points in the production for good products. Shinetec dryer has the construction such as hot air being flow controlled hot air in width direction can be supplied on the material. Also, for infrared radiant heater shall be checked for each in the test operation in our factory, and temperature of the heater face is taken with balance photos after checking the balance situation, we will supply it will built-in so our instruments are trusted by all means.
Shinetec's Top Zone of vertical treater can be cooled at 30-40oC in order to proof the resin adhesion.
We would like to inform this advantage reason why we adopt the 3-rollers system top roller. And so please kindly understand it's merit.
- Material tension cut between dryer's wet zone and dry zone.
- Prevent the material slipping at top zone. Due to support the material by means of 3-roller system, it can be easily controlled stable speed without material's slipping.
- Be reduced as much as difference of treatment condition on both side of the material surface. ( In case of only one side touching, it easily occur the creases due to retrenchment of material and resins.
* Rotary cutter and Piling unit |
Cutting size able to be set in select switch method with a quick changeover device (4-stages).
Low speed cutting and thin-object cutting possible.
As piling unit is equipped with special air blow system that used Ionized air, stable piling is possible for the material of 25-210 g/m2 weight.
And as the side guide plates, one side jogger mechanism is equipped and consideration is paid for prevention of the trouble for the time of material inserting and improving the piling accuracy.
Zig-zag piling can be executed. This greatly serves to automatization of the following processes until the pressing process.
- Piling Device -
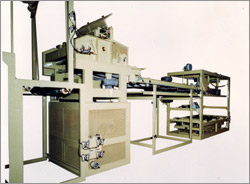
- Other equipment (Splice Press Unit)
The material can be connected in turn with adhesive in the following direction automatically and in right direction without leaning to one side, and not causing distortion locally such as shifting or slippage etc. and can be dawn out continuously. We have new type splice press unit with carrier mechanism.
|
|
|
|
. |